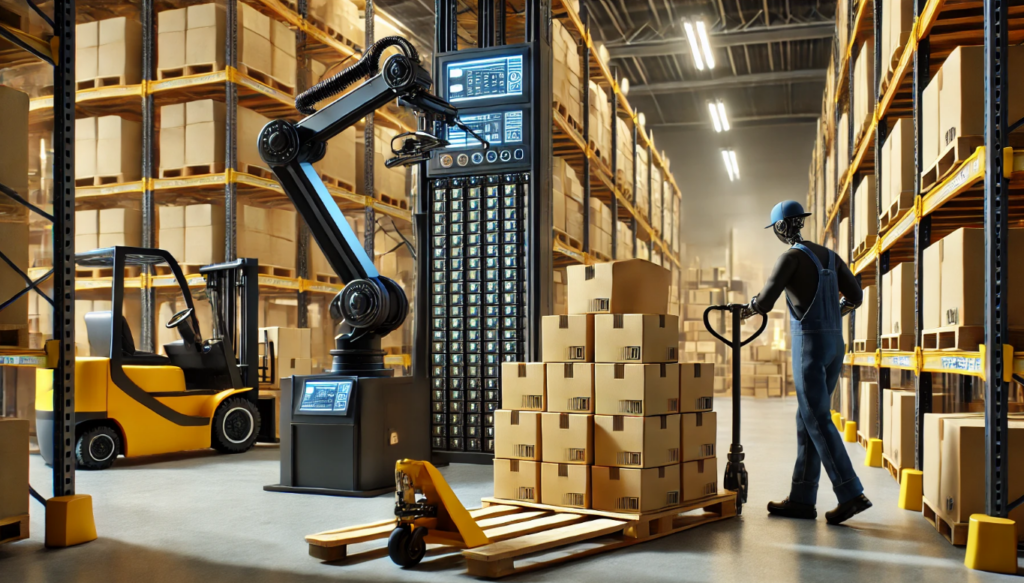
In today’s fast-paced world, efficient material handling is crucial for warehouses and food production facilities. Proper handling not only ensures efficiency but also safeguards workers and product quality.
Challenges in Material Handling
Moving heavy and bulky loads poses significant challenges. Manual handling often leads to inefficiencies, potential damage, and increased costs. Overcoming these challenges requires robust solutions.
Alternative Solutions to Material Handling:
- Conveyor Systems: Reduce manual lifting and transport materials efficiently across a facility.
- Forklifts and Pallet Jacks: Essential for moving heavy loads quickly and safely.
- Automated Guided Vehicles (AGVs): Transport materials autonomously, improving efficiency and reducing labor costs.
- Cranes and Hoists: Ideal for lifting and moving extremely heavy items with minimal strain on workers.
- Ergonomic Lift Assist Devices: Help reduce strain on workers by providing mechanical assistance for lifting and positioning loads.
Human Limitations and Safety Concerns
Relying on human effort for heavy lifting has its limits. Physical strain and the risk of injury are high, making it essential to invest in solutions that protect workers and maintain productivity.
According to the National Institute for Occupational Safety and Health (NIOSH), the recommended maximum weight for manual lifting under ideal conditions is 51 pounds (23 kg). However, this limit decreases depending on factors such as lifting height, distance from the body, and repetition. In many workplaces, lifting loads above 35 pounds (16 kg) without assistance is discouraged to reduce the risk of injury.
The Role of Automation in Material Handling
Automation, like the palletizing solutions from UltimateRobotics.com, is transforming material handling. These innovations enhance efficiency, reduce human error, and boost safety.
One of the key advantages of robotic palletizing is the significant increase in speed. A manual palletizing process can typically handle around 5-8 cases per minute, depending on the weight and complexity of the task. In contrast, robotic palletizing systems can operate at speeds of 20-30 cases per minute, representing a 3-4 times increase in efficiency. This speed improvement not only enhances throughput but also reduces bottlenecks in production, ensuring a smoother and more cost-effective operation.
Tools and Equipment for Efficient Handling
Investing in the right tools and equipment is vital. From automated systems to specialized machinery, these investments pay off through improved efficiency and worker well-being.
The Benefits of Hand Trucks and Dollies
Hand trucks and dollies play a crucial role in material handling by reducing the physical strain on workers and improving productivity. These simple yet effective tools allow workers to transport heavy and bulky loads with minimal effort, decreasing the risk of injury and fatigue. Key benefits include:
- Enhanced Safety: Reduces the chances of musculoskeletal injuries by minimizing heavy lifting.
- Increased Efficiency: Enables workers to move multiple items at once, reducing the time spent on transportation.
- Versatility: Suitable for various industries, including warehousing, food production, and retail.
- Cost-Effective: A low-cost investment that significantly improves workflow and reduces labor costs.
- Ergonomic Design: Many models are designed with adjustable handles and lightweight yet durable materials, making them easy to use in different environments.
Cost Analysis for Robotic Palletizing Machine
A robotic palletizing machine costs between $70,000 and $120,000. The average annual salary for a warehouse worker in Florida is about $30,225. Assuming a worker works full-time and the facility operates in three shifts (24/7), here’s how the cost breaks down:
- Annual Cost per Worker (3 Shifts): $30,225 × 3 = $90,675
- Payback Period (Years): Machine Cost / Annual Cost per Worker
Calculations:
- For a $70,000 machine: $70,000 / $90,675 ≈ 0.77 years (about 9 months)
- For a $120,000 machine: $120,000 / $90,675 ≈ 1.32 years (about 16 months)
Flexion Point: For facilities with at least three workers per shift dedicated to palletizing, the break-even point for investing in a robotic palletizing machine is approximately 9 to 16 months, depending on the machine’s cost. This investment not only boosts efficiency but also ensures a safer, more productive work environment.
Conclusion
Efficient material handling is more than a convenience—it’s a necessity for workplace safety, productivity, and cost savings. Implementing automation and proper lifting techniques can prevent injuries, reduce operational expenses, and enhance workflow in warehouses and food production facilities.
Leave a Reply